Dielectric fluids provide two functions that are essential to proper transformer operation
- An insulating function that prevents an electric arc from forming between live parts
- A cooling function by circulating the fluid through the exchangers (passive radiators, cooling system, etc.)
These dielectric fluids are usually oils (mineral, plant, silicone, ester and synthetic) and deteriorate due to:
- moisture content
- the formation of dissolved gases
- the presence of impurities
- oil oxidation
This deterioration alters the dielectric specifications of each fluid. As replacing the oil is expensive and not very eco-friendly, Arras MAXEI proposes recycling solutions:
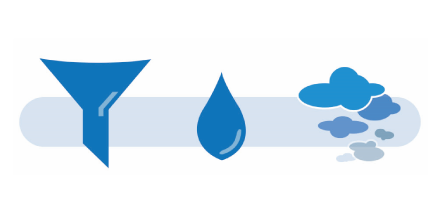
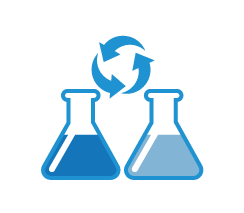
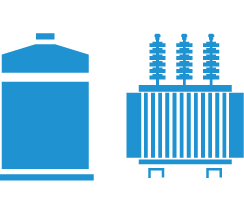
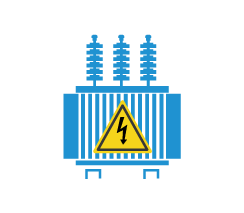
Processing oil consists in purifying it by evaporating the water and the dissolved gases in a vacuum. Our machine processes make it possible to combine low operating costs, excellent performance levels and high levels of reliability.
We propose 2 lines of processing machines from 300 to 12,000 litres/hour, but which can go much further depending on client requirements.
The Xe-Lean line is suitable for processing the oil from a tank. It is excellent value for money, performance and quality.
The MAS is more effective. It is mainly designed for service providers and meets specific requirements.
Performances:
- Conditions: standard quality mineral oil (distillation curve of 0.01 mb at 80°C) with 50 ppm of water and 10% de dissolved gas in a single passage at an input temperature of 70°C minimum
- Water content 10 times lower (between 5 and 10 ppm)
- Dissolved gas content divided by almost 100 (less than 0.1%)
- Breakdown voltage higher than 75 kV
Service imperatives and network characteristics sometimes make shutting down a transformer to process its oil problematic. A running transformer solution, known as Live Processing is a real advantage in those cases, but requires maximum control and reliability at each step.
In order to allow the processing when the transformer is running, we propose the MAS TEC line of machines. These machines carry out the same moisture removal, degassing and filtering processes as a MAS type machine, but with an additional specific highly secure connection system.
Its automated control system controls each step from connection to disconnection to prevent any operator errors. During these critical phases, the least entry of air or gas into the oil circuit could lead to the instant and damaging breakdown of the running transformer.
For operator safety, the connection system to the tank must be at a sufficient distance from the terminals and other live parts.
Processing oil consists in purifying it by evaporating the water and the dissolved gases in a vacuum. Our machine processes make it possible to combine low operating costs, excellent performance levels and high levels of reliability.
We propose 2 lines of processing machines from 300 to 12,000 litres/hour, but which can go much further depending on client requirements.
The Xe-Lean line is suitable for processing the oil from a tank. It is excellent value for money, performance and quality.
The MAS is more effective. It is mainly designed for service providers and meets specific requirements.
Performances:
- Conditions: standard quality mineral oil (distillation curve of 0.01 mb at 80°C) with 50 ppm of water and 10% de dissolved gas in a single passage at an input temperature of 70°C minimum
- Water content 10 times lower (between 5 and 10 ppm)
- Dissolved gas content divided by almost 100 (less than 0.1%)
- Breakdown voltage higher than 75 kV
Service imperatives and network characteristics sometimes make shutting down a transformer to process its oil problematic. A running transformer solution, known as Live Processing is a real advantage in those cases, but requires maximum control and reliability at each step.
In order to allow the processing when the transformer is running, we propose the MAS TEC line of machines. These machines carry out the same moisture removal, degassing and filtering processes as a MAS type machine, but with an additional specific highly secure connection system.
Its automated control system controls each step from connection to disconnection to prevent any operator errors. During these critical phases, the least entry of air or gas into the oil circuit could lead to the instant and damaging breakdown of the running transformer.
For operator safety, the connection system to the tank must be at a sufficient distance from the terminals and other live parts.
The oil deteriorates, becomes acid and turns a brownish colour. At this stage there is a real danger to the transformer as the breakdown voltage deteriorates quickly.
The regeneration process is an economic and eco-friendly alternative to changing the oil. It avoids using a large quantity of new oil and the need to manage the used oil. It reduces oil acidity, dibenzyl disulphide content and the regeneration of the oil without having to shut down the installation.
Oil regeneration is a process used to recover the original physical-chemical specifications (acidity, colour, viscosity, resistivity, IFT, tab delta, oxidation resistance, breakdown voltage, dibenzyl disulphide/corrosive sulphur, etc.) by passing through resins commonly know as “Foulon’s earth”. Between each cycle, these resins are reactivated using a high temperature process (300 reactivations) before the resin specifications are deteriorated.
The combustion fumes can be processed using activated carbon before being released. Several solutions are currently being developed, such as catalysis, thus making it possible to eliminate waste and have more effective fume processing.
The REGEN system can be proposed:
- As a complete unit, combining oil processing and regeneration units on a single frame for better space occupation (container fitted with technical access hatches and a control cabin for the operators)
- As a separate regeneration module to be used downstream of an existing processing system
REGENs can house all the options available for oil processing (some may be fitted as standard)
Many catalogue or specific options can be used to adapt each machine to your needs:
- Protection and mobility (trailer, tarpaulin , bodywork, etc.)
- Control and safety (monitoring, remote monitoring, safety cut-off valve, instrumentation, process monitoring, etc.)
- Strengthened functions (heating, strengthened vacuum, additional connections, etc.)
- Ergonomic accessories
- Measurement devices (water content, breakdown, activity, etc.)
